>> Challenges and Innovations for Medical Device Packaging
Medical Devices and Primary Package Types
Medical devices encompass a wide range of instruments, apparatuses, and implants designed for diagnosing, preventing, monitoring, or treating medical conditions. They vary from simple tools like thermometers and bandages to complex equipment such as pacemakers and injection devices, including syringes and prefilled injectors.
Primary packaging plays a vital role in protecting medical devices, ensuring sterility, and maintaining compliance with FDA regulations. Medical device packaging must be designed to withstand sterilization processes, preserve product integrity, and facilitate safe handling. Several types of primary medical device packaging are commonly used:
- Pouches: Flexible, heat-sealed, or self-sealing pouches for surgical instruments and disposable tools.
- Rigid Trays: Custom-molded plastic trays that provide secure containment and aseptic presentation for delicate devices.
- Wraps: Non-woven barrier materials used to wrap surgical kits and prevent contamination.
- Blister Packs: Typically transparent, semi-rigid enclosures that ensure single-use sterility and tamper evidence, commonly used for syringes, injection devices, and prefilled drug delivery systems.
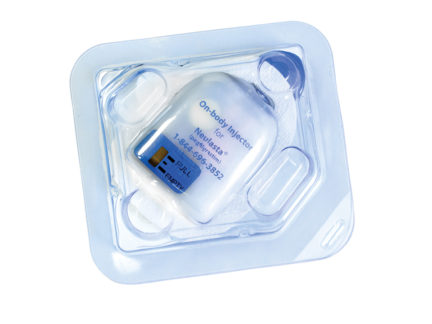
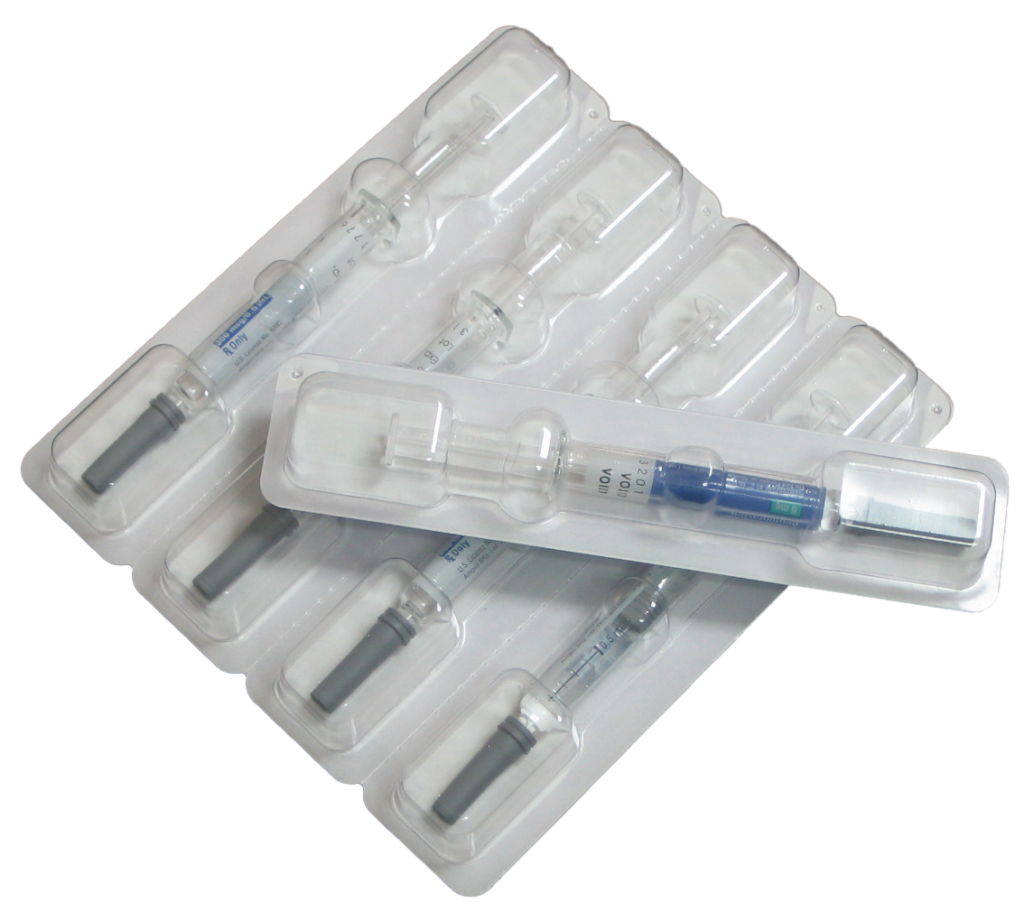
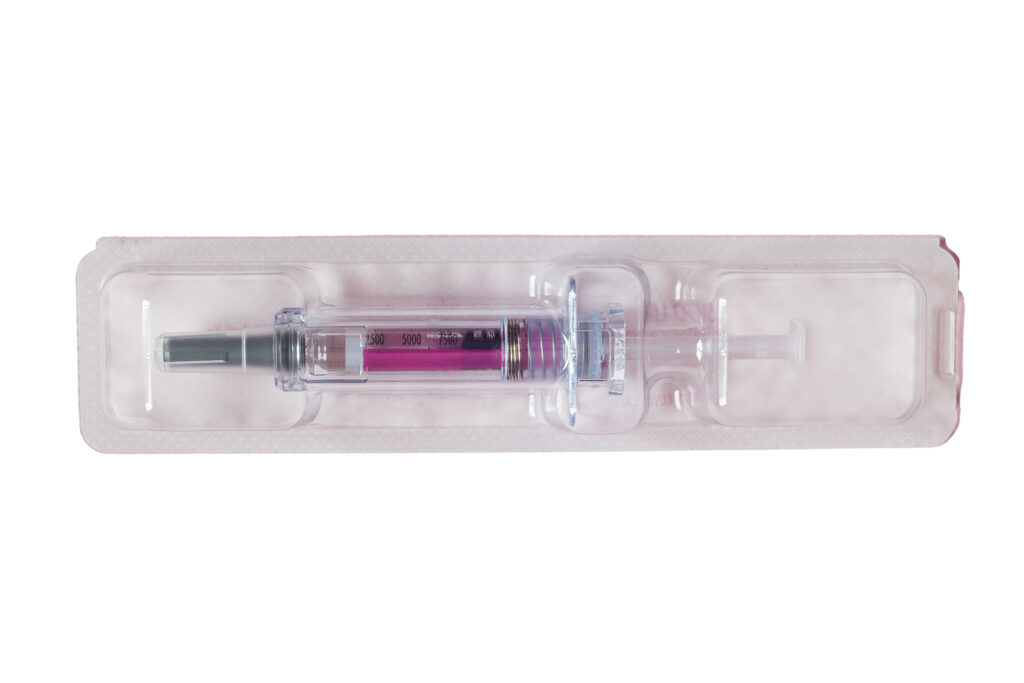
Though blister packaging is not the predominant format for medical devices, it has gained traction across healthcare packaging applications and has already established itself as a preferred option for some medical device categories.
It is no secret that Pharmaworks specializes in blister packaging equipment and solutions tailored for the pharmaceutical, nutraceutical, and medical industries. Our advanced thermoforming equipment is designed to meet stringent sterility, safety, and regulatory requirements, ensuring high-quality packaging across healthcare applications.
Pharmaworks has worked with multiple clients from the medical device industry and has a proven track record producing packaging solutions commonly used for:
- Syringes & Injection Devices
- Suture Kits & Surgical Tools
- Nasal Sprays & Nasal Atomizers
- Wearable Medical Devices & Pumps
Pharmaworks integrates automation, inspection, and feeding systems to enhance medical device packaging efficiency, ensuring compliance with industry standards, and supporting manufacturers in innovation and sustainability efforts.
How Medical Device Blister Packs Differ from Solid Dose Applications
Medical devices differ significantly from pharmaceutical products in their size, shape, functionality, and handling requirements. Unlike oral tablets or capsules, which are uniform in size and shape, medical devices range from simple syringes to suture kits and complex wearable devices or multi-component surgical tools. As such, there are unique characteristics to take into consideration:
- Varied Sizes & Shapes: Medical devices do not have standardized dimensions, requiring custom packaging solutions to accommodate everything from small injection devices to larger surgical tools and diagnostic equipment.
- Multi-Component Kits: Some medical devices include multiple parts, such as test kits, combination drug-device systems, or surgical kits, which must be securely packaged together.
- Strict Sterility Requirements: Many devices require absolute sterility, meaning their packaging must withstand various sterilization methods like ethylene oxide (EtO), gamma radiation, or autoclaving without compromising protection.
- Tamper Evidence & Safe Handling: Packaging must ensure product integrity, providing clear tamper-evident features while also facilitating ease of use in hospital or clinical environments.
How Blister Packaging Accommodates These Unique Needs
To address these challenges, blister packaging for medical devices incorporates larger formats, deeper cavities, and multiple forming processes:
- Larger Blister Formats: Devices such as syringes, injection pens, and surgical tools require expanded blister dimensions and secure containment while maintaining structural integrity.
- Deeper Cavities for Complex Devices: Wearable medical technology, auto-injectors, and other medical devices demand deep thermoformed cavities to accommodate their unique geometries.
- Multi-Component Kits: Custom blister designs allow for the secure placement of multiple device components, ensuring that kits remain organized. Sometimes package requirements call for snap-in features formed right in the blister to secure the product.
- Material Selection: High-strength plastics such as PETG or medical-grade PVC provide durability and sterility, supporting various sterilization techniques while protecting the device from damage. Both base (forming) and lid (sealing) materials vary depending on the required sterilization requirement for the medical device.
Sterilization Methods for Blister Packaging
Sterilization Method | Potential Materials |
Gamma Radiation | PETG, Polycarbonate, Polyethylene, Tyvek® |
Ethylene Oxide (EO) | Tyvek®, Polyethylene, PETG |
Autoclaving (Steam) | Polypropylene, Nylon, Tyvek®, Medical Paper |
*Always refer to material manufacturer specifications for compatible sterilization methods.
Base Materials for Medical Device Blister Packaging
Materials respond differently to heat and pressure, necessitating precise controls and proper training to ensure optimal results. Common materials used for medical device blister packaging include:
- PETG (Polyethylene Terephthalate Glycol): A widely used medical-grade plastic known for its clarity, strength, and compatibility with EtO and gamma sterilization.
- PVC (Polyvinyl Chloride): Offers rigidity and cost-effectiveness, commonly used for single-use medical packaging.
- PP (Polypropylene): Provides chemical resistance and flexibility, ideal for heat-sealed blister applications.
- Cold Form Foil (Aluminum-Based): Used for high-barrier protection, preventing moisture and oxygen exposure for sensitive medical products.
Pharmaworks Blister Forming Methods
Pharmaworks specializes in blister packaging solutions that can accommodate the unique requirements of medical devices, as previously mentioned, accommodating larger forming sizes and deeper cavities. Our blister package forming technology ensures precise forming of cavity shapes and sizes, using air, plug assist, and cold form methods to achieve optimal packaging integrity. Key features include:
- Maximum Forming Dimensions and Depth: Pharmaworks’ blister machines support a range of different blister sizes and depths needed for larger medical devices.
- Air & Plug Assist Technology: Multiple Pharmaworks machine models utilize servo-driven plug assist systems to ensure uniform cavity depth and precise forming, optimizing packaging for complex medical devices.
Cold Form Capabilities: All Pharmaworks’ blister machines support cold forming applications, providing enhanced barrier protection for sensitive medical products.
Blister Machine Model Specifications
Model | Max Forming Area | Thermoform Max Depth | Cold Form Max Depth |
TF3 | 220 mm x 290 mm | 40 mm | 17.5 mm |
TF2 | 160 mm x 290 mm | 40 mm | 17.5 mm |
TF1pro | 120 mm x 165 mm | 25 mm | 15 mm |
TF1e | 90 mm x 165 mm | 25 mm | 15 mm |
TF1 | 90 mm x 165 mm | 25 mm | 10 mm |
BlisterMate | 220 mm x 290 mm | 40 mm | 20 mm |
*All specifications are dependent upon blister packaging application.
Pharmaworks Temperature and Forming Controls
Pharmaworks has specialized in blister machines and thermoformers since its inception. Our control system and HMI technology provide users with the controls needed to fine-tune the blister forming process.
- Preheat Station Technology: All Pharmaworks machines feature a Preheat Station that heats materials to user-specified temperatures and provides independent upper and lower plate temperature controls. Users can also set temperature thresholds that will trigger an alarm and stop the process, ensuring quality control.
- Servo-Driven Forming Adjustments: Users can set forming depth right from the HMI when using plug assist and cold form since both utilize servo-driven systems for precision.
- Hands-On Training & Troubleshooting: Pharmaworks’ experienced service techs provide hands-on training and guidance, equipping operators to identify and troubleshoot forming inconsistencies, material defects, and process variations. Additionally, Pharmaworks offers online training, allowing operators to work through common troubleshooting scenarios at their own pace.
Other Considerations
The focus of this article has been on the physical blister —forming, materials, and dimensions. However, successful blister packaging for medical devices depends on more than just forming the blister package itself. Some other key aspects must be considered:
- Product Handling: Ensuring precise feeding and placement of medical devices within blister cavities while maintaining sterility.
- Inspection Systems: Utilizing vision systems and automated checks to detect defects, ensure correct alignment, verify print and codes, and validate packaging integrity.
- Blister Transfer & Downstream Equipment: Managing the transport of larger-format blisters efficiently, integrating conveyor systems and robotic handling for smooth transitions.
We’ll explore those topics and more in later articles. In the meantime, head over to Pharmaworks.com to learn more about each Pharmaworks blister machine model and other blister packaging solutions.
For more Pharmaworks news, click here.