Over the past year, WLS has been doing their part to curb the COVID-19 pandemic. A leading packaging equipment manufacturer, WLS of ProMach Pharma Solutions is supplying their VR-72 Labeler to COVID vaccine manufacturers and contract packers. Worldwide opportunities continue to present themselves as the pharmaceutical industry pushes to fulfill the demand for approved vaccines.
“We’ve been extremely busy supporting COVID vaccine manufacturers and their vendors. After trade shows were unfortunately cancelled last year, we were able use that turn of events to divert our VR-72 labeler demo machines to customers who urgently needed them,” said Philippe Maraval, V.P. of Business Development at WLS. “Since then, we’ve been building up our inventory and now have stock labelers ready for the next surge of demand. Depending on the customization needed, we are currently able to ship these labelers to customers in significantly less time than usual.”
Fully servo-driven with a modular design, this continuous-motion, pressure-sensitive solution codes and applies wrap-around labels at speeds well in excess of 600 vials per minute.
“COVID vaccine manufacturers have been asking us for a few different options that we can now provide. Our VR-72 can be equipped with 2D code printing or RFID tags application to improve serialization and tracking. It can also apply thermochromic labels, small round labels that change color if the packages undergo a temperature change — signaling a quality control issue,” said Maraval. “Our COVID vaccine customers need labelers that not only run reliably at high-speeds but have the flexibility to easily adapt to ever-changing requirements such as vial size and/or coding, quality control and anti-counterfeiting features.”
In addition to vaccines, the VR-72 is ideal for a variety of pharmaceuticals, nutraceuticals and medical devices. It applies paper or film pressure-sensitive labels to vials, bottles, syringes, auto-injector devices and other cylindrical packages. The VR-72 is available with a variety of code printing methods, inspection systems and other options including redundant label heads and more.
Overall, the VR-72 provides high-speed operation, accurate and repeatable label placement, low maintenance and quick changeovers with only one change part.
Read the press release to learn more about this best-in-class labeler and feel free to contact your regional sales manager here: https://www.weilerls.com/contact/wls-sales-territories.
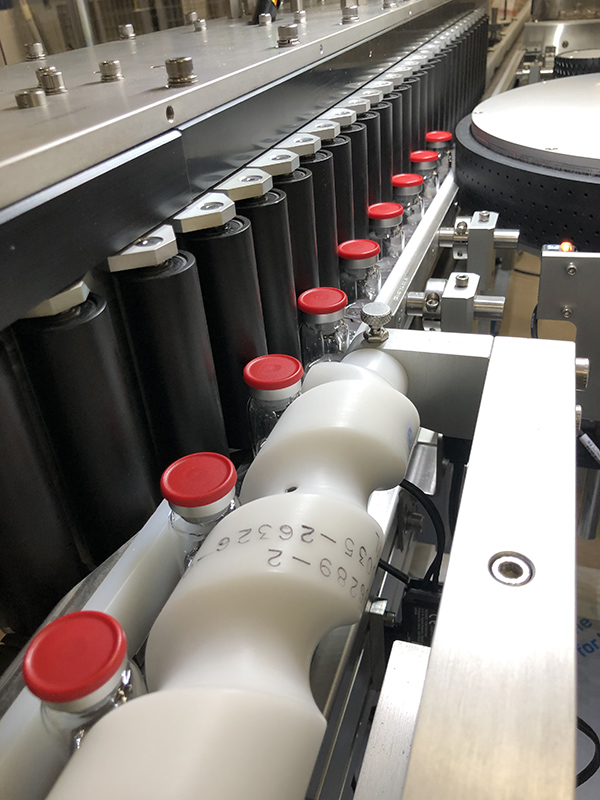